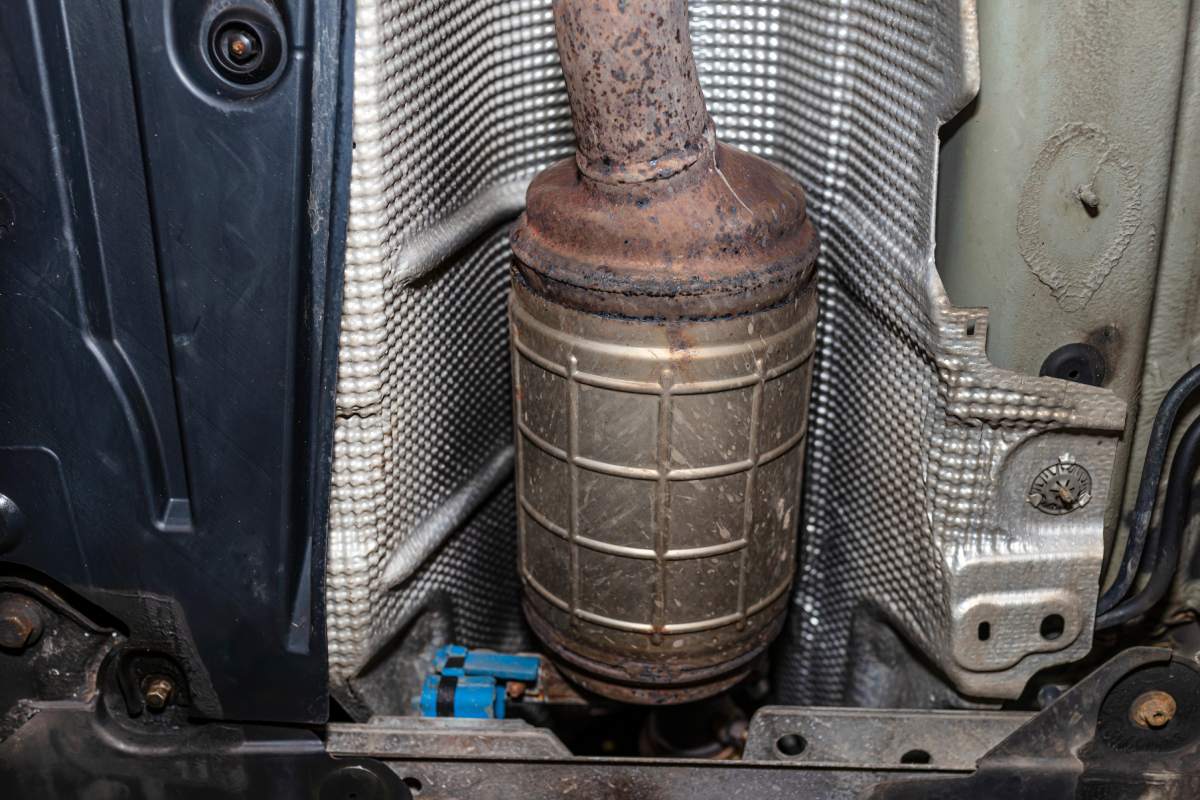
Selective Catalytic Reduction (SCR) technology is an advanced and highly effective method used to reduce nitrogen oxide (NOₓ) emissions from the exhaust gases of combustion sources such as power plant boilers, gas turbines, and other industrial equipment.
NOₓ gases contribute significantly to air pollution, forming smog, acid rain, and fine particulates harmful to human health and the environment. SCR systems use chemical reactions to convert NOₓ into harmless nitrogen (N₂) and water (H₂O) through a catalytic process involving ammonia as a reducing agent.
How SCR Systems Work
SCR systems operate by injecting ammonia (NH₃) or its derivatives into the exhaust gas upstream of a catalyst. The injected ammonia reacts selectively with NOₓ in the presence of oxygen (O₂) on the catalyst surface, following these chemical reactions:
- 4NH₃ + 4NO + O₂ → 4N₂ + 6H₂O
- 2NH₃ + NO + NO₂ → 2N₂ + 3H₂O
- 4NH₃ + 2NO₂ + O₂ → 3N₂ + 6H₂O
The catalyst typically consists of base metals like titanium or vanadium oxides, zeolites, or noble metals. Its design maximizes surface area and optimizes flue gas flow for efficient reactions while minimizing pressure drop within the system.
Key Components of an SCR System
- Catalyst Bed: Facilitates the chemical reactions between ammonia and NOₓ.
- Ammonia Injection System: Precisely injects the reducing agent (ammonia, aqueous ammonia, or urea) into the flue gas.
- Mixing Mechanisms: Ensures uniform distribution of ammonia and NOₓ for optimal reaction efficiency.
- Control Systems: Monitor parameters such as temperature, flow rate, and ammonia slip (excess ammonia in emissions).
SCR Design and Operating Considerations
Temperature Range
The effectiveness of the SCR process depends heavily on maintaining the appropriate operating temperature:
- Base-metal catalysts: Operate efficiently between 200°C and 425°C.
- Zeolite-based catalysts: Function at higher temperatures, up to 600°C.
Catalyst Geometry
Catalysts often feature a honeycomb design, balancing the need for a large surface area and low obstruction to gas flow. This configuration minimizes pressure drops and maintains system efficiency.
Reagent Options
Three forms of ammonia delivery are commonly used:
- Anhydrous Ammonia: Most cost-effective but hazardous to handle.
- Aqueous Ammonia: Safer but increases operational costs due to water vaporization requirements.
- Urea Solutions: Safer still, though requiring additional hydrolysis equipment, leading to higher initial costs.
Advantages of SCR Technology
- High NOₓ Reduction Efficiency: SCR can achieve up to 90% or higher reduction in NOₓ emissions, making it suitable for stringent environmental regulations.
- Selective Reaction: The technology exclusively targets nitrogen compounds without affecting other components like sulfur or carbon oxides.
- Scalability: Applicable across a wide range of industries, from small-scale biomass plants to large coal-fired power plants.
Challenges and Limitations
- Ammonia Slip: Excess ammonia in the exhaust stream, if not managed properly, can form secondary pollutants.
- High Initial Costs: The capital investment for catalysts and injection systems can be significant.
- Maintenance Needs: Catalyst deactivation due to fouling or poisoning by contaminants like sulfur may require periodic replacement or cleaning.
Applications of SCR Technology
SCR systems are widely used in industries such as:
- Power Generation: Coal, natural gas, and biomass power plants.
- Petroleum Refining: To meet strict NOₓ emissions standards.
- Waste-to-Energy Plants: For handling exhaust gases with high particulate content.
SCR vs. Selective Non-Catalytic Reduction (SNCR)
A related technology, Selective Non-Catalytic Reduction (SNCR), also reduces NOₓ emissions by injecting ammonia-based reagents directly into the combustion zone. However, SNCR achieves lower reduction rates (30–50%) compared to SCR (up to 90%) and operates at much higher temperatures (900°C–1,000°C). SCR is the preferred choice for industries requiring significant NOₓ reductions.
Future of SCR Technology
As regulatory agencies impose increasingly strict emission limits, SCR technology continues to evolve. Modern innovations include:
- Advanced Catalysts: Designed for ultra-low NOₓ emissions and high durability.
- Integrated Systems: Combining computational modelling and optimized designs to fit complex industrial setups.
- Renewable Energy Integration: Supporting cleaner emissions in renewable energy plants and hybrid systems.
SCR’s role in addressing air pollution and climate change challenges underscores its importance in global environmental protection efforts
This detailed examination of SCR technology highlights its critical role in reducing harmful emissions, ensuring compliance with environmental standards, and paving the way for cleaner industrial processes.